Shrinkproofing Wool: A Quick Primer
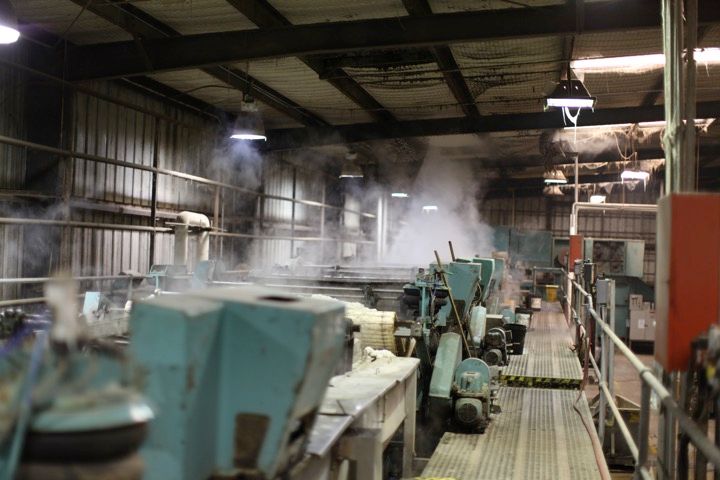
Love it or hate it, but machine-washable wool has kept the wool industry afloat.
Hello, wool-curious humans!
Last week I told you about a study that suggested machine-washable wool biodegrades three times faster than untreated wool and without releasing any microplastics. Since then, I received a very reasonable question from a reader. "That's great news," she said. "But how do they even make wool machine-washable in the first place?"
Excellent question! Here's a brief overview.
There is no single, universally practiced process for shrinkproofing wool. But the current standard is a chlorine-polymer shrink-resist sytem called the "chlorine Hercosett" process. This involves exposing the fibers to a dilute chlorine solution (about what you'll find in a swimming pool, which may explain why pools are so terrible on our hair) and then sealing the fibers with a crosslinked polyamide resin known as Hercosett 125.
This all takes place long before the wool has been made into a yarn, fabric, or product. If the wool is processed in accordance with Woolmark standards, it can be called Superwash.
Let's start with the washing.
The Scouring Train
Standard wool scouring lines, or trains, will have six enormous "bowls" of hot water through which one continuous mass of wool is moved. (I put that in quotes because, really, these are giant tanks.) The first three bowls contain soapy water for scouring. The second three have clear water for rinsing.
The wool travels through high-pressure rollers that extract as much liquid as possible before the wool moves into the next bowl. Giant steel harrow "rakes" keep everything moving forward. They dip their teeth into the water, nudge the wool forward, and then lift out, always remaining perfectly perpendicular to the water. Imagine bicycle pedals going around and around, but always pointing straight down.
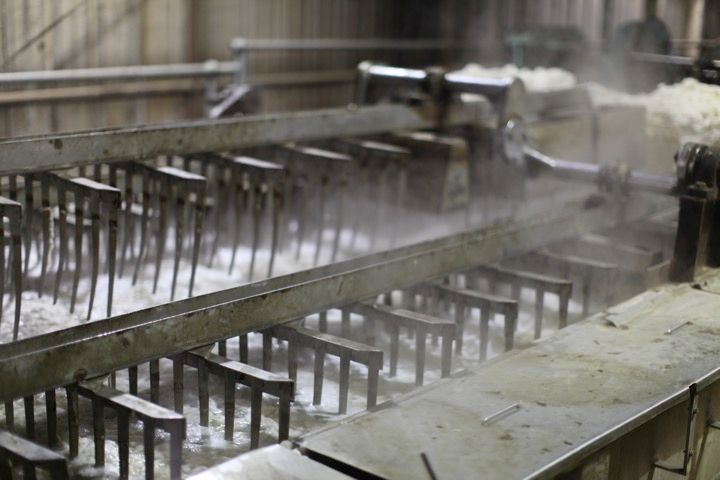
Now for the Hercosett
This step involves two high-level processes, the bleach and the polymer. These take place across five suction drum bowls, all of which are much smaller than those in the scouring line. Some can have six bowls, which I'll explain.
First, the wool is run through a dilute bleach solution (a chlorine compound called sodium hypochlorite). Then, to neutralize the bleach so that it stops eating the wool fibers, the wool is moved through a solution of metabicarbonite and bisulphite. At this point, the outermost layer of the wool fiber has been successfully nibbled away and a negative charge has been generated on the wool's surface that makes it more receptive to the polymer.
Five-bowl systems will only have one rinse bowl at the end of these two steps. The six-bowl systems, like at Chargeurs, will have a rinse bowl after the first step as well.
Now, the wool is run through the two finishing steps: the Hercosett resin to seal the fiber surface again, and a softener to give everything a happy send-off. It's rather like applying hair conditioner after you've gotten out of the pool and rinsed your hair.
From there, the wool goes through the drum dryer and is bundled up and ready to go to the mill!
Even after the polymer begins to wear off, your chances of a dramatic felting accident are still lowered because the original scales (which enmesh and cause felting) have been buffed down by the bleach. But do note that over time, machine-washability may degrade. Fortunately, wool doesn't need to be laundered very often.
And that, my friends, is a very abbreviated overview of the most common form of shrinkproofing wool. It's worth noting that the U.S. currently has one scouring facility that offers this service, Chargeurs.
Inside Chargeurs
My friend and esteemed wool mentor, Dr. Lisa Surber, was lucky enough to tour Chargeurs a few years ago. She has graciously given me permission to share her photos of the process here. She has also shared her knowledge of the process with me.
Chargeurs does the shrinkproofing in a separate area after the wool has been scoured, dried, blown, carded, and combed into top.
Not only is Chargeurs the only place to process machine-washable wool in this country, but it's also our only remaining commercial topmaker. This means that basically any domestic product containing combed, worsted-spun wool came through Chargeurs. Offshoring has left our textile manufacturing infrastructure in an extraordinarily fragile place.
Drawbacks and Alternatives?
The main downside to the chlorine-polymer process is that it requires lots of water (to fill all those bowls) and potentially polluting agents, which can easily find their way into our rivers and groundwater. Some manufacturers dispose of far cleaner wastewater than others, and we now know that the Hercosett-125 polymer doesn't chip off and form microplastics in water. Still, it's cause for concern.
Textile scientists have been working for the last decade to develop “greener” machine-washable wool processes that require less energy and generate less pollution. A few have entered mainstream production and gained GOTS certification: EXP and plasma.
EXP (named for Ex-Pollution) uses natural enzymes and biopolymers to do the work of the chlorine and Hercosett, but still using water. A promising process out of Japan is Life Fibre EFT, which uses an "interfacial polymerization" to effectively eliminate the bleach stage.
The plasma process, on the other hand, produces no wastewater and uses no chemicals, just a mix of non-polluting electrons, ions, and free radicals. But plasma requires a tremendous amount of electricity to produce, and the results have questionable longevity.
Most of these alternate processes have yet to gain widespread adoption because of higher costs, slower production times, and greater risks of negative impact to the fiber's texture, receptivity to dye, and tensile strength. But work continues.
Even in the realm of the proven, no treatment is 100% foolproof. The Woolmark "gold" standard for machine washability (TM-31) still allows for up to 5% shrinkage in length and width. As with any good material derived from living beings, wool will always need to carry a small percentage of mystery. That's part of the magic, right?